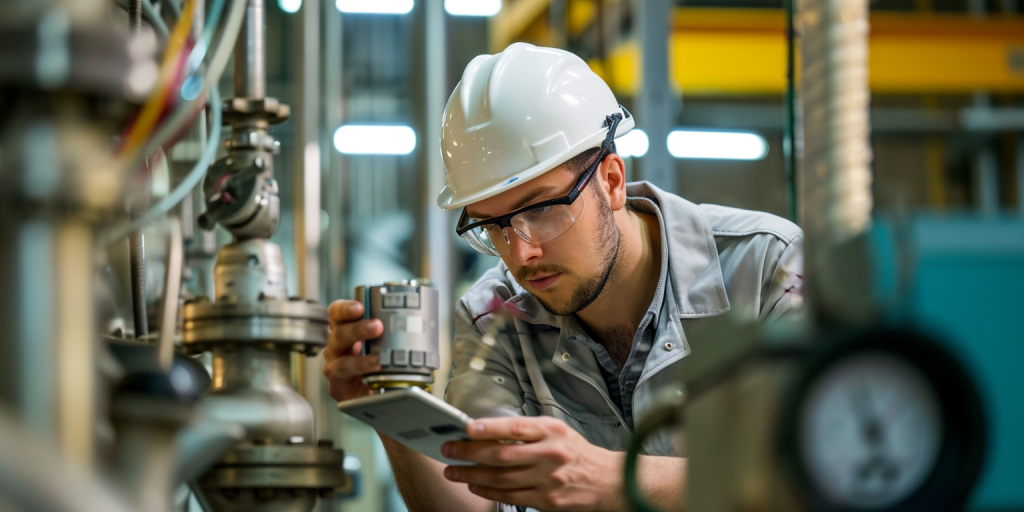
Accurate flow measurement is crucial across various industries, including manufacturing, energy, and healthcare. To maintain precision and reliability, flowmeters—devices that quantify fluid flow—must undergo regular calibration. This article examines the importance of calibration, shares best practices, and addresses the key challenges in maintaining flowmeter accuracy.
The Significance of Calibration
Calibration is the act of comparing a flowmeter’s output to a known standard to validate its accuracy. Getting flow measurement right is crucial for effective process control, quality assurance, and compliance with environmental and safety requirements. Regular calibration ensures that flow data is trustworthy and compliant with industry guidelines.
Best Practices in Flowmeter Calibration
-
Regular Calibration: Schedule calibration at suitable intervals, based on the meter type, usage, and working environment, to account for drift and wear.
-
Traceability: Ensure calibrations are traceable to official national or international standards. Using ISO/IEC 17025-accredited laboratories can guarantee consistency.
-
Proper Handling: Follow manufacturer instructions to protect flowmeters from damage or contamination during transportation, installation, and calibration.
-
Environmental Conditions: Maintain stable temperature, pressure, and humidity during calibration to minimize external influences on accuracy.
-
Standardized Procedures: Use a documented, standardized calibration method. Include all necessary pre-checks, adjustments, and post-calibration verification.
-
Thorough Record Keeping: Document calibration outcomes, dates, technician names, and any necessary adjustments – critical for both quality control and compliance.
Challenges in Flowmeter Calibration
-
Fluid Properties: Accurate calibration can be complicated by changing fluid characteristics, such as temperature, viscosity, and density—lab conditions may not always match real-world operations.
-
Wear and Degradation: All flowmeters deteriorate over time, which can impact accuracy. Periodic recalibration offsets gradual drift.
-
In-Situ Calibration: For some critical installations, removing the meter isn’t practical. Portable or master meters enable in-place calibration as a solution.
-
Multi-Variable Instruments: Flowmeters that measure several variables simultaneously (mass flow, temperature, pressure) add calibration complexity due to the variable interdependence of these variables.
-
Cost and Downtime: Calibration may be expensive and require process interruption. Careful scheduling and backup meters help minimize these downsides.
-
Non-Repeatability: Low-flow meters may be hard to calibrate due to fluctuations; advanced statistical analysis can help overcome these issues.
Conclusion
Regular, well-documented calibration is crucial for maintaining the accuracy and reliability of flowmeters. By adopting best practices and proactively tackling common challenges, organizations can safeguard the integrity of their flow data—supporting tighter process control, better product quality, and regulatory compliance. Ongoing improvements in calibration technology and methods only enhance these capabilities further, ensuring flow measurement keeps pace with industry needs.